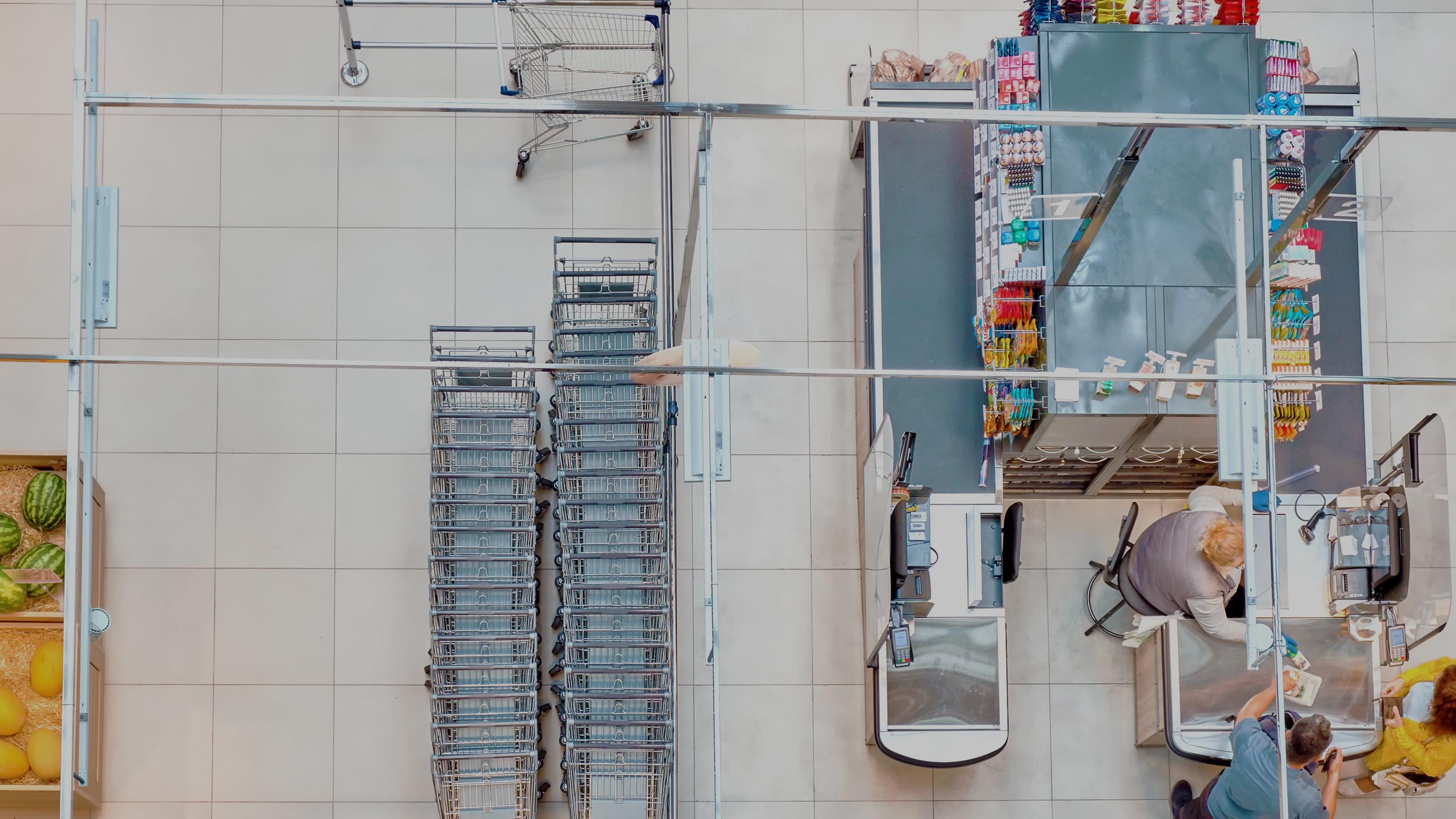
Bullwhip-Effekt: Nachfrageschwankung durch Corona
In volatilen Zeiten wie in der aktuellen Corona-Krise verändert sich die Nachfragesituation signifikant, teils unvorhersehbar…
Blogreihe Produktionsoptimierung
Die kontinuierliche Optimierung von Produktionsprozessen ist weit mehr als nur ein kurzfristiges Mittel zur Stärkung der Marktposition. Vielmehr ist es eine lebenslange Aufgabe, die Produktionskosten und Durchlaufzeiten dauerhaft nachhaltig zu senken – bei gleichbleibend hoher Produktqualität. In unserer Blogreihe „Produktionsoptimierung“ zeigen wir Ihnen zentrale Handlungsfelder auf und geben Ihnen praxisnahe Strategien an die Hand, mit denen Sie Ihre Wettbewerbsfähigkeit langfristig steigern können.
Haben Sie einen klaren Überblick darüber, wie sich Ihre produktspezifischen Herstellkosten zusammensetzen? Wissen Sie, welche die drei größten Kostentreiber in Ihrer Fabrik sind oder welche Maßnahmen Sie sofort ergreifen können, um kosteneffizienter zu produzieren? Falls nicht, sind Sie nicht allein: Zahlreiche Unternehmen, branchenübergreifend, stellen sich genau diese Fragen, um langfristig wettbewerbsfähig zu bleiben. In diesem Beitrag erfahren Sie, wie Sie relevante Handlungsfelder sichtbar machen, die wichtigsten Stellschrauben identifizieren und gezielt Ihre Produktionskosten senken können.
Trotz der zunehmenden Individualisierung von Produkten – und der damit verbundenen Komplexität – zählen die Produktionskosten nach wie vor zu den größten Herausforderungen im produzierenden Gewerbe. Der Kaufpreis eines Produkts bleibt ein entscheidender Faktor für die Kaufentscheidung, wodurch die Herstelleinzelkosten eines jeden Produkt einen maßgeblichen Einfluss auf den Unternehmenserfolg nehmen. Doch wie gelingt es, diese Kosten langfristig niedrig zu halten? Vielen Unternehmen fällt es schwer, effektiv Maßnahmen zu identifizieren und umzusetzen. Häufig mangelt es an Transparenz – entweder wird gar nicht eingegriffen oder es werden falsche Maßnahmen definiert. Damit Sie diese Fehler vermeiden, zeigen wir Ihnen im Folgenden einen strukturierten Weg, wie Sie gezielt und nachhaltig Ihre Produktionskosten senken können.
Daten sind der Schlüssel zu klarer Kostentransparenz. Wer sie systematisch erfasst und gezielt einsetzt, sichert sich in Zukunft einen entscheidenden Wettbewerbsvorteil.
Johannes Rauh, Senior Berater
Für viele produzierende Unternehmen ist nicht vorhandene Transparenz eine zentrale Herausforderung. Oft ist unklar, wie die spezifischen Herstellkosten je Produkt, Abteilung oder Produktionslinie genau zustande kommen oder wann diese die Deckungsbeiträge gefährden. Ein Grund dafür ist die unzureichende Erhebung und Nutzung von umfangreichen Prozess- und Materialdaten. Ohne fundierte Datenbasis, klar definierte Kennzahlen und aussagekräftiges Reporting ist das tatsächliche Kostenbild oft nicht ersichtlich. Falls Ihnen bislang Unternehmensdaten fehlen, bietet die Nutzung moderner IT-Systeme großes Potenzial. Durch die Integration Ihrer Geschäftsprozesse und die Speicherung der erzeugten Daten liefern beispielsweise ERP-Systeme eine solide Basis für weiterführende Analysen.
Ein bewährtes Instrument zur Identifizierung und Bewertung von Kostenkomponenten ist die Cost Breakdown Analysis. Typischerweise lassen sich Produktionskosten in fixe und variable Anteile aufteilen. Variable Produktionskosten umfassen beispielsweise Aufwendungen für Energie (z.B. Glas- oder Stahlindustrie), Material (z.B. Halbleiter- und Bauindustrie) und direktes Personal (z.B. Maschinen- und Anlagenbau). Zu den Fixkosten zählen Abschreibungen für Gebäude, Maschinen und Anlagen sowie Kosten für das indirekte Personal. Fixkostenintensive Branchen sind unter anderem die Lebensmittel- und Chemieindustrie, da sich hier häufig ein fortgeschrittener Automatisierungsgrad und damit überproportional hohe Kosten für Maschinen und Anlagen finden.
Ein weiterer Ansatz zur Ermittlung der tatsächlichen Produktionskosten ist der Total Cost of Ownership (TCO) Ansatz. Ziel dieser Methode ist die Betrachtung sämtlicher Kosten über den gesamten Produktlebenszyklus, um ein ganzheitliches Bild der Kostenstruktur zu zeichnen.
Dadurch erhalten Sie unmittelbar eine Roadmap zur Optimierung der Datenqualität optimieren, auf deren Basis Sie bessere Analysen entwickeln können. Sind die Produktionskosten einmal transparent aufbereitet und mit den Experten der unterschiedlichen Fachbereiche, insbesondere Controlling und Produktion, validiert, folgt im nächsten Schritt, die Identifizierung der größten Kostentreiber. Damit kann der Fokus Ihrer tiefgreifenderen Analysen auf das wesentlichen Bereiche gelegt werden.
Sind die wichtigsten Kostentreiber identifiziert, besteht der nächste Schritt darin, deren Ursachen genau zu analysieren und gezielt Maßnahmen zur Kostensenkung abzuleiten. Denn gerade in der Produktion ist es eine kontinuierliche Aufgabe, Ineffizienzen aufzudecken und zu beheben.
Im klassischen Maschinenbau oder der Elektroindustrie gibt es auch heute noch vielerorts manuelle Tätigkeiten, die entweder nicht effizient durchgeführt, wie etwa das Anziehen des Drehmoments mit einem manuellen Schlüssel, oder unnötigerweise wiederholt werden (z.B. Prüfung oder Justage). In der Prozessindustrie, beispielsweise in der Glas- und Pharmaindustrie, entstehen steigende Kosten häufig durch veraltete Anlagen oder überflüssige Prozessschritte.
Diese nicht-notwendigen Verschwendungen, im Lean Management mit dem japanischen Wort „Muda“ bezeichnet, gilt es, mittels einer strukturierten Methodik zu identifizieren. Rothbaum setzt hierbei auf bewährte Methoden, wie etwa Wertstromanalysen, Multi-Moment-Aufnahmen oder Process Mining. Insbesondere durch die Kombination analoger- und digitaler Analysemethoden kann ein ganzheitliches Bild über Ihre Prozesse und darin vorkommende Verschwendungen gezeichnet werden. Eine zentrale Rolle nimmt das vorhandene Wissen Ihrer Mitarbeiter ein. Erst durch die Kombination der langjährigen Expertise Ihres Teams mit Best-Practices aus unseren Projekten identifizieren wir optimale Lösungen.
Doch die reine Ermittlung von Verschwendungen reicht nicht aus. Erst mittels Definition klarer Maßnahmen inklusive Umsetzungsroadmap wird sichergestellt, dass sich die Optimierungen auch messbar in Ihren Herstellkosten widerspiegeln. Neben der Automatisierung manueller Tätigkeiten (Vorsicht bei der Rentabilitätsrechnung, Stichwort TCO) können Sie auf die vielseitigen Werkzeuge des Lean Managements zurückgreifen, um wirksame Verbesserungen zu realisieren. Auch hier setzen wir auf aktive Einbindung Ihrer Mitarbeitenden. So ist es uns beispielsweise im Sondermaschinenbau gelungen, durch die Umstellung von manueller Werkstattfertigung auf eine getaktete Fließmontage die Montagekosten pro Maschine um bis zu 50 % zu senken.
Wenn Sie auf der Suche nach Unterstützung sind, um Ihre Produktion kosteneffizient und zukunftsträchtig aufzustellen, kommen Sie auf uns zu!
Insbesondere dort, wo die Automatisierung als Optimierungsmaßnahme an ihre Grenzen stößt, ergeben sich im produzierenden Gewerbe weitere Schwierigkeiten. Energieintensive Branchen, wie beispielsweise die Glasherstellung oder Hightech-Fertigungen in der Halbleiterindustrie, stehen aufgrund stark gestiegener Energiekosten unter erheblichem Druck. Neben der bereits erwähnten Prozesseffizienz gibt es weitere Hebel, um Unternehmen zukunftsfähig aufzustellen. Durch verbesserte Planungs- und Steuerungsprozesse, gestützt von modernen IT-Systemen, kann die Anlagenauslastung gezielt optimiert werden. Folglich lassen sich Leerläufe reduzieren und Hochfahr- oder Rüstprozesse minimieren.
Bei unserem Kunden vandaglas konnten wir dadurch Potenziale sichtbar machen und einen besonders energieintensiven Arbeitsbereich hinsichtlich Betriebszeit und Kosten gezielt verbessern. In Kombination mit einer firmeneigenen Photovoltaik-Anlage lassen sich zusätzliche Einsparungen erzielen – etwa durch die gezielte Nutzung energieintensiver Maschinen zu Zeiten hoher Sonneneinstrahlung. Das senkt nicht nur die Kosten, sondern steigert zugleich die Energieeffizienz.
Energieintensive Branchen stehen weiterhing auch wegen der gestiegenen Materialkosten vor gemeinsamen Herausforderungen. Die Preise für knappe Rohstoffe wie seltene Erden, die in der Halbleiterindustrie unverzichtbar sind, sind gestiegen. Lieferengpässe infolge globaler Krisen, wie der Blockade des Suezkanals, verschärfen die Situation zusätzlich. Daher ist es essenziell, die Optimierung der Materialkosten gezielt in den Fokus zu rücken. Neben alternativen Materialien oder Verhandlungserfolgen im Einkauf lohnt sich ein genauer Blick auf die Produktion. Ein Optimierungshebel der Ressourcennutzung ist die kontinuierliche Reduzierung von Ausschuss, dass ohnehin teure Materialien entweder nur durch zusätzliche Aufwände wiederverwendet werden können oder gar gänzlich entsorgt werden müssen.
Mit Maßnahmen zur Fehlervermeidung wie „Poka Yoke“ aus dem Lean Management oder statistischer Prozesskontrolle (SPC) lässt sich der Ausschuss minimieren. Darüber hinaus bieten sich weitere Einsparpotenziale bereits in der Beschaffung und Produktionssteuerung: Durch strategische Lieferantenwahl und Just-in-time-Anlieferungen können Lagerbestände gezielt verringert werden. Somit werden die Lagerhaltungskosten sowie das Working Capital reduziert.
Die Reduzierung von Verschwendung in der Produktion ist kein einmaliges Projekt, sondern ein fortlaufender Prozess. Kontinuierliche Verbesserung muss daher langfristig und nachhaltig gedacht werden.
Philipp Kappus, Senior Manager
Selbstverständlich darf bei allen Maßnahmen zur Effizienzsteigerung das Kundeninteresse nicht aus dem Blick geraten. Die Zufriedenheit Ihrer Kunden wird klassischerweise anhand des sogenannten magischen Dreiecks aus Kosten, Qualität und Lieferzeit beschrieben. Wir bei Rothbaum ergänzen dieses Modell um zwei weitere Kenngrößen: Flexibilität und Nachhaltigkeit. Alle fünf Faktoren stehen in direkter Wechselwirkung zueinander. Höhere Anforderungen an Qualität oder Lieferzeit führen häufig zu steigenden Kosten – umgekehrt kann eine reine Fokussierung auf Kostensenkung zulasten von Qualität oder Service gehen. Unser Ziel ist es, Ihre Produktionskosten senken, ohne dabei negative Auswirkungen auf einen der anderen Faktoren zu erzielen.
Gleichzeitig können sich allerdings auch zu hohe Ansprüche negativ auf Ihre Herstellkosten auswirken. Übermäßige Qualitätskontrollen in Bereichen, in denen kaum Fehler auftreten, verursachen unnötige Kosten – ebenso wie über-optimierte Produktdesigns mit zum Beispiel zu engen Toleranzen oder teuren Materialien, die vom Kunden kaum wahrgenommen werden. Ein bekanntes Beispiel sind optimierte Spaltmaße in der Automobilindustrie. Durch bewusste Entscheidungen, Leistungsumfänge zu reduzieren, Kontrollen zu verringern oder weniger hochwertige Materialien zu verwenden, können große Einsparungen erzielt werden.
Zusammenfassend lässt sich sagen: Der erste Schritt, um nachhaltig Produktionskosten zu reduzieren, liegt im Aufbau einer transparenten Datengrundlage. Auf dieser Basis lassen sich anschließend die größten Kostentreiber identifizieren, Schwachstellen gezielt analysieren und wirkungsvolle Maßnahmen entwickeln. Durch optimale Abstimmung auf Ihre Kundenbedürfnisse schaffen Sie es anschließend, nachhaltigen Geschäftserfolg zu erreichen. Wenn Sie auf der Suche nach Unterstützung sind, um Ihre Produktion kosteneffizient und zukunftsträchtig aufzustellen, kommen Sie auf uns zu!
Senior Berater, Frankfurt
Unter anderem hat er bereits Projekte in den Bereichen Global Footprint, Standortsuche, Fabrik- und Logistikplanung begleitet. Sein Fokus liegt dabei auf den Geschäftsfeldern Produktion und Logistik, für welche auch das Thema Nachhaltigkeit besonders relevant sind.
Sie sehen gerade einen Platzhalterinhalt von Facebook. Um auf den eigentlichen Inhalt zuzugreifen, klicken Sie auf die Schaltfläche unten. Bitte beachten Sie, dass dabei Daten an Drittanbieter weitergegeben werden.
Mehr InformationenSie sehen gerade einen Platzhalterinhalt von Instagram. Um auf den eigentlichen Inhalt zuzugreifen, klicken Sie auf die Schaltfläche unten. Bitte beachten Sie, dass dabei Daten an Drittanbieter weitergegeben werden.
Mehr Informationen